マネジメントサイクルとは?種類別の機能の解説と事例を紹介
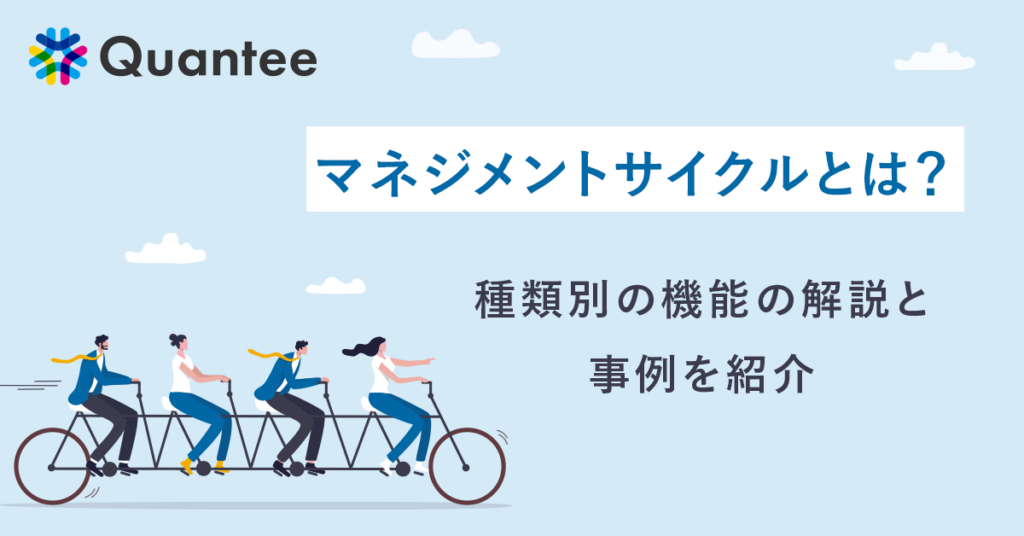
企業が目標を達成するために欠かせないのが、マネジメントサイクルです。そう言われても、マネジメントサイクルがどのような意味で、どんな使い方をしたらいいのか分からない方もいるでしょう。
そこで今回は、目標達成を目指している経営者向けに、マネジメントサイクルの機能と事例について解説していきます。目標達成のために業務の効率化を図りたい方は、最後まで読み進めてみてください。
マネジメントサイクルの基本
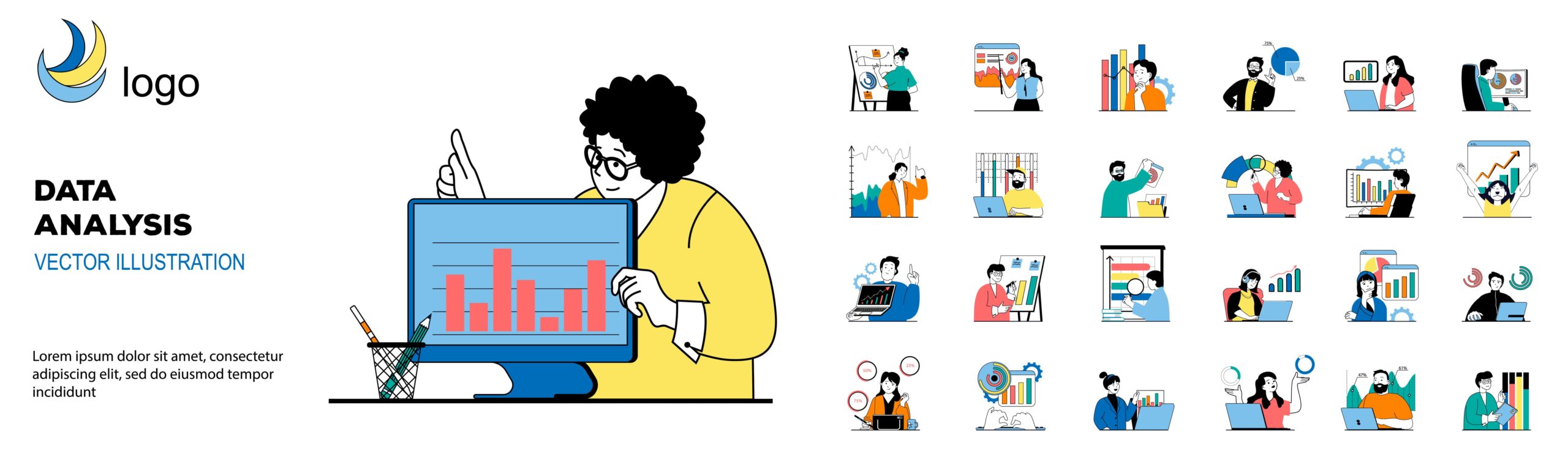
まずは、基本となるマネジメントサイクルについての解説です。
マネジメントサイクルがどういう仕組みなのか、なぜ重要なのかについて、それぞれ詳しく解説していきましょう。
マネジメントサイクルとは
マネジメントサイクルは、企業が目標達成に向けて業務改善をおこなう際に活用する仕組みです。
マネジメントサイクルは、基本的に以下の流れでおこなわれます。
- 計画
- 実行
- 改善
まずは計画です。どのような目標を設定するかを決めないと、その後の行動ができません。
目標が決まったら、次はその目標に向けて行動します。行動を続けていくと、何かしらの問題や気づきが生まれるでしょう。
次の改善では、その問題や気づきを洗い出します。改善をおこなうことで、行動がより洗練されて目標達成に近づけます。
マネジメントサイクルを活用すると、行動の精度を高めるサイクルが生まれて、効率よく目標達成ができるでしょう。
マネジメントサイクルの重要性
マネジメントサイクルは、市場の変化が激しい現代では必須の仕組みです。
顧客や市場が常に変化していくので、常に同じ考えや同じ行動を繰り返していてはニーズを把握できなくなるためです。
- 目標を設定する
- 目標に向けて行動する
- 行動を評価して改善する
上記のプロセスを取り入れて、常に変化する市場に適応していきましょう。
マネジメントサイクルとISMS
ISMS(Information Security Management System)は、情報セキュリティマネジメントシステムの略称です。情報マネジメントシステム認定センターによると、ISMSの役割は以下の通りです。
- 必要なセキュリティレベルを決める
- プランを持ち、資源を配分する
- システムを運用する
このISMSには、マネジメントサイクルの代表格であるPDCAが組み込まれています。PDCAを含め、マネジメントサイクルにはさまざまな種類が存在します。
マネジメントサイクルの種類
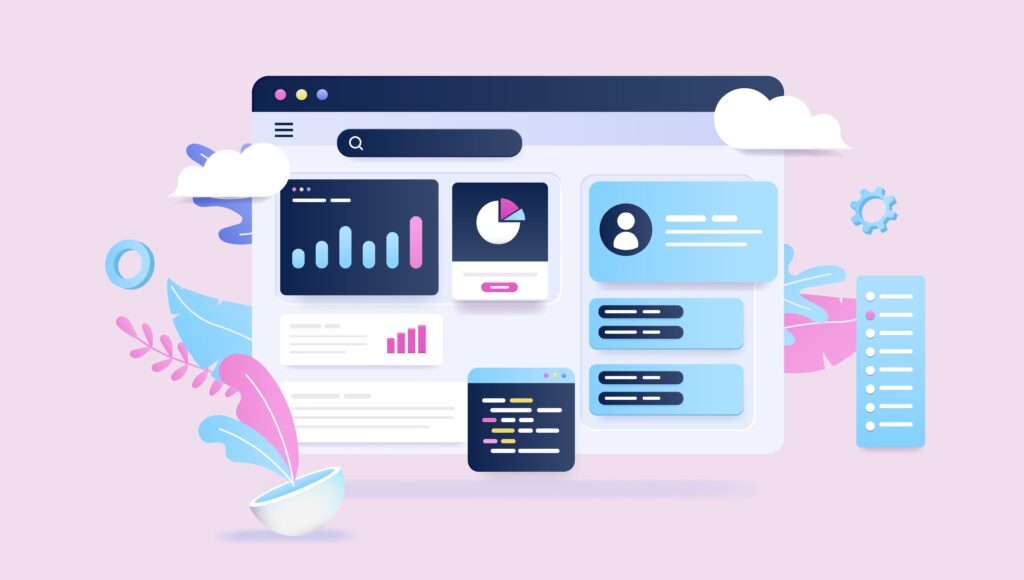
目標達成に役立つマネジメントサイクルの種類をまとめてみました。
- PDCA
- OODA
- PDR
- CAPD
- PDS
- STPD
それぞれのマネジメントサイクルの特徴について、詳しく解説していきましょう。
PDCA
PDCAとは、アメリカの統計学者「W・エドワーズ・デミング」が発見しました。
PDCAは以下の4つのプロセスの頭文字をとった名称で、マネジメントサイクル界でもっとも有名な仕組みです。
- Plan(計画)
- Do(実行)
- Check(評価)
- Act(改善)
PDCAは、目標や課題に対して計画を立て、実行し、その結果や効果を評価し、改善策を講じるという一連の流れを継続的におこないます。
PDCAは、業種や職種を問わずに適用できる汎用性の高い仕組みなので、日本では品質管理部門を中心に多くの企業や部門で採用されています。
OODA
OODAは、アメリカ空軍の戦術家「ジョン・ボイド」が開発しました。OODAは、以下のプロセスの頭文字をとったマネジメントサイクルです。
- Observe(観察)
- Orient(方向付け)
- Decide(決定)
- Act(行動)
OODAの特徴は、計画がない点です。その代わりに観察を設けて、現場の現状把握に重きを置いています。現状に重きを置くことで、常に起きる問題にいち早く対応できる点がメリットです。
競争が激しく常に変化し続ける現場では、PDCAよりもOODAの採用が増えてきました。
PDR
PDRは、ハーバード大学の「リンダ・A・ヒル」が提唱したマネジメントサイクルです。以下のプロセスの頭文字を集めて、PDRと呼ばれています。
- Plan(計画)
- Do(実行)
- Review(振り返り)
PDRはPDCAと同様に、「計画→実行→評価」によって品質や効率の向上を図ります。PDCAとの違いは、評価をおこなう際に振り返りを適用する点です。
振り返りをおこなうことで、行動や成果に対して学びや新たな気づきを得られます。PDCAよりも工数が少ないので、より短時間でマネジメントサイクルを回せます。
CAPD
CAPDとは、以下の行動の頭文字をとったもので、現場主義のマネジメントサイクルです。
- Check(確認)
- Act(改善)
- Plan(計画)
- Do(実行)
気づいた方もいるかと思いますが、先に紹介したPDCAの順番を変えたのがCAPDです。最初に現場の状況や問題を確認してから改善をおこない、後に計画と実行をおこないます。
現場主体でのマネジメントサイクルなので、計画と現場のミスマッチが少ない点と、サイクルを回しやすい点がメリットです。
製造業など、現場に多くの人員を配置している企業では、CAPDの方が効率よくマネジメントサイクルを回せるでしょう。
PDS
PDSとは、PDCAを短縮したようなマネジメントサイクルです。PDSは、以下のプロセスの頭文字が由来です。
- Plan(計画)
- Do(実行)
- See(観察)
PDCAのCheckとActをSeeに集約することで、より短いサイクルで業務改善を可能にしました。
サイクルが短い反面、Seeでのプロセスが多くなるデメリットもあるので、規模の小さな業務や少人数の部署に適しています。
STPD
STPDは、ソニーに勤務していた「小林茂」氏が提唱したと言われているマネジメントサイクルです。
STPDは、以下のプロセスの頭文字から構成されています。
- See(現状把握)
- Think(現状分析)
- Plan(計画立案)
- Do(実行)
現状把握と分析で多くのデータを収集、分析してから計画立案するので、より緻密な計画を作成できる点が特徴です。そのため、事業計画などの重要事項を決定する際に役立つでしょう。
マネジメントサイクルの事例
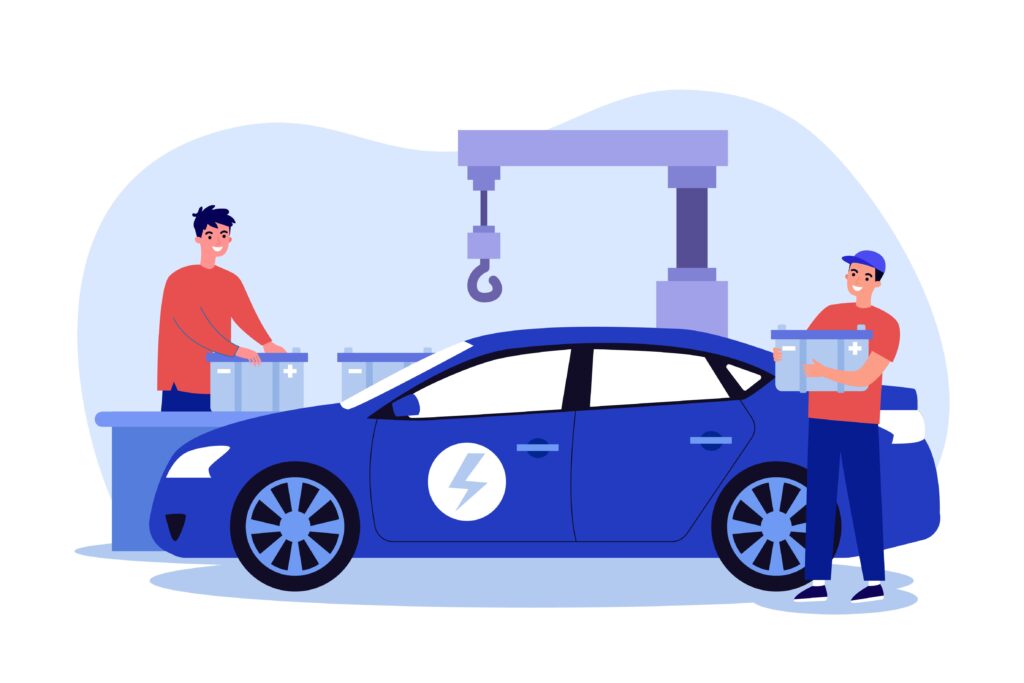
マネジメントサイクルの事例として、今回はトヨタ自動車株式会社を紹介していきます。
トヨタ自動車株式会社は、世界的な自動車メーカーです。トヨタ自動車株式会社では、「トヨタ生産方式」と呼ばれる独自のマネジメントサイクルを採用しています。
トヨタ生産方式は、以下の4つのプロセスで構成されています。
- カイゼン
- 問題の見える化
- なぜなぜ分析
- 7つのムダどり
トヨタ自動車株式会社では、「より良いものを、より早く、より安く」を目標に改善活動をおこなっています。カイゼンは、欠点を改善するという意味ではなく、現場の作業効率を良くするという意味です。
トヨタ自動車株式会社は、カイゼンを通してより効率よく作業ができる環境、より安全な環境を作って生産性を高めています。
問題の見える化では、トラブルを共有するのが目的です。現場でトラブルが起きた際は作業を中断し、知恵を出して改善活動をおこなうルールになっています。
その問題を突き止める際にはなぜなぜ分析を使用し、原因の真相を追求します。真の原因が分からないと、正しい改善活動ができないためです。
そして、トヨタ自動車株式会社では、以下の7つのムダとりを徹底しています。
- つくりすぎのムダ
- 手持ちのムダ
- 運搬のムダ
- 加工のムダ
- 在庫のムダ
- 動作のムダ
- 不良をつくるムダ
上記のムダを省くことで、常に生産性を高める努力を怠りません。
これが、世界中で採用されているトヨタ自動車株式会社独自のマネジメントサイクルです。
マネジメントサイクルにおすすめのツール
ここまで、事例を交えてマネジメントサイクルが重要な理由を解説してきました。しかし、手作業でマネジメントサイクルを回していくのは簡単ではありません。
そんなときに役立つのが、KPI(重要業績評価指標)マネジメントツールの「Quantee」です。
Quanteeは、以下の特徴を持っています。
- KPI進捗管理からPDCAまでを仕組化する
- 組織、メンバー、施策ごとの課題を可視化する
- 各種データの集計と管理を一元化する
施策別や現場のKPIをまとめて管理し、それぞれのPDCAサイクルを適切に回せるので、大幅な業務の効率化が図れます。
マネジメントサイクルを採用したいけれど人材が足りない、やり方が分からないと悩んでいる企業は、一度Quanteeの詳細を確認してみてください。
マネジメントサイクルは専用ツールを使って効率化できる
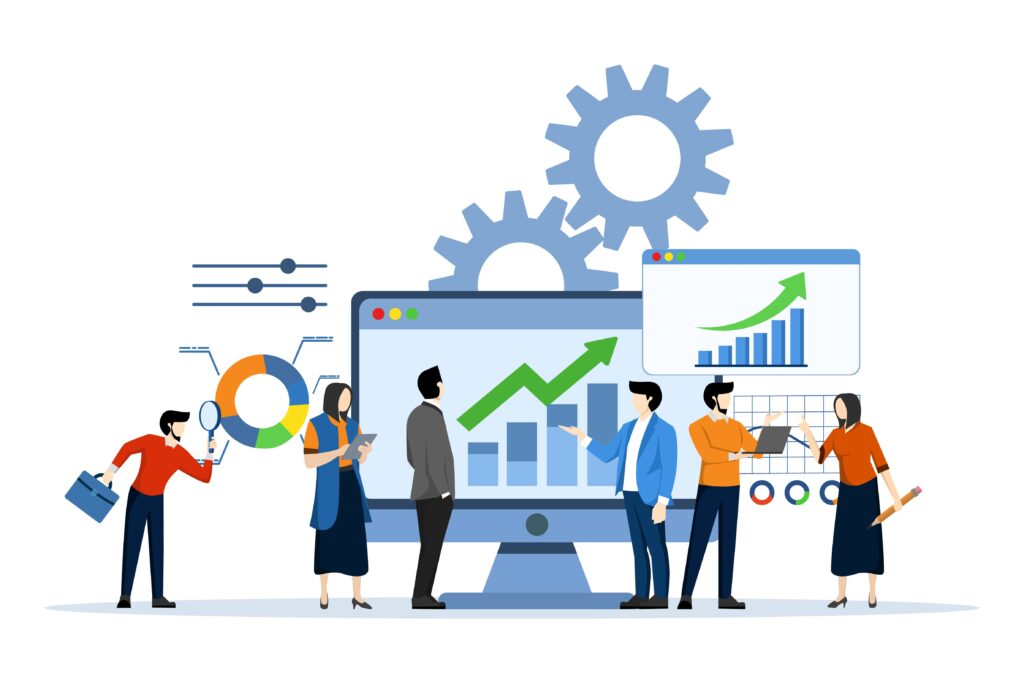
マネジメントサイクルは、業務の効率化を図り目標達成するために欠かせない仕組みです。マネジメントサイクルには複数の種類があるので、自社の業務に適したものを選んでみましょう。
マネジメントサイクルのやり方が分からない企業は、専用ツール「Quantee」の導入をおすすめします。Quanteeは全てのデータを一元管理し、PDCAサイクルを自動で回してくれます。
なかなか目標達成ができていない企業は、ツールを活用して目標達成を実現してみてください。